WHO ARE WE?
ECO CLEANING WIPES BULGARIA LTD is a leading company in the production of cotton cleaning cloths from recycled textiles, by mechanically removing all metal parts and manually cutting rags following the practices of the most stringent industry standards. Founded only in 2019 by a team with many years of experience in the field of collection, sorting and recycling of clothing and other textiles, the company manages to establish itself as a market leader due to its expertise, new generation production facilities ensuring excellent production quality and capacity of over 1000 tons per year.
In order to provide a variety of items for our customers, as well as to maintain high quality products, we work only with the best suppliers in Europe, such as Switzerland, the Netherlands, Germany and Bulgaria. Our products are intended for both the local market and for export - our central warehouse and the production itself is located in the heart of Bulgaria – the town of Plovdiv, but for your convenience we can arrange delivery to anywhere in Europe.
The range of goods in stock exceeds 10 types and covers a wide variety of items for different industries, with an option for packaging of 2.5 kg, 5 kg and 10 kg. The quality of the goods is guaranteed by internal standards and criteria set out in the management of all processes proven in our many years of practice - from delivery and sorting to their cutting, packaging and shipping to the customer.
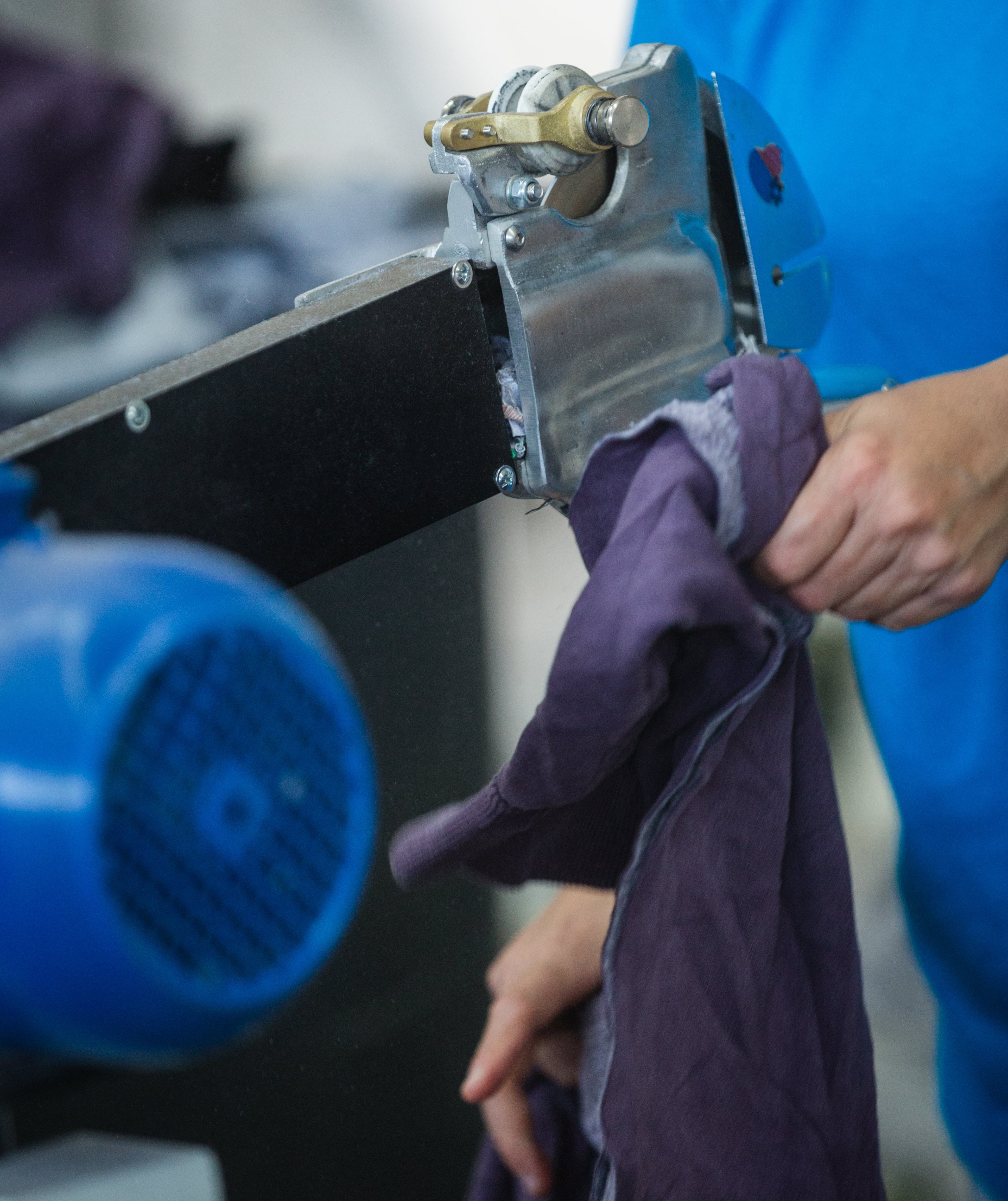
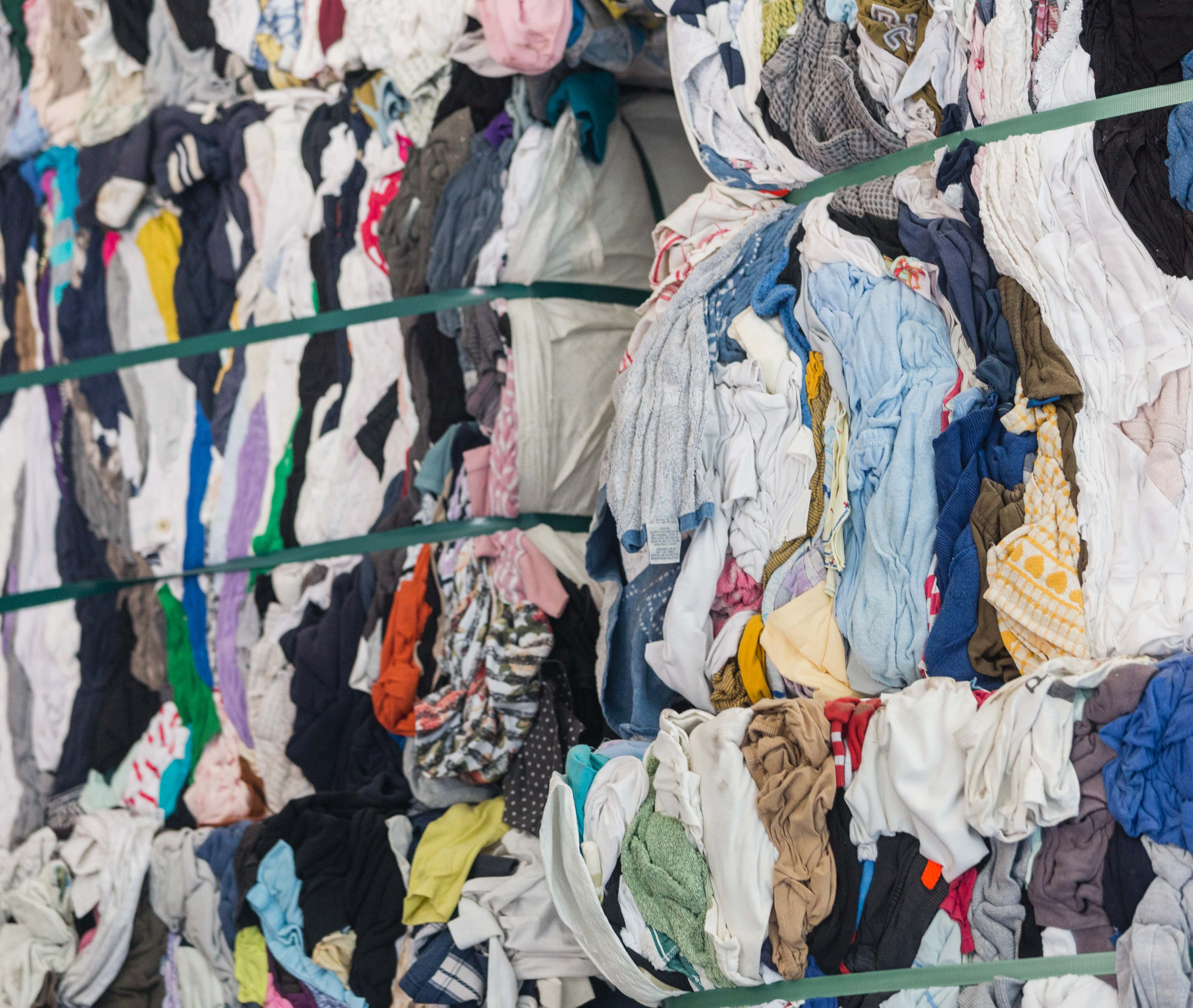
WHAT WE DO?
Used clothes and other textiles are a valuable material that should not end up in landfills. Reuse is the most environmentally friendly way to extend the life of the textile, as it requires the least additional resources and energy. The collected clothes are sorted and disinfected and according to their condition are sold to the second hand markets. In most of the usable clothes there is a certain amount of textile waste, which is unfit for use in the form of clothes, but can be used as rags.
These are cotton fabrics, which are an indispensable consumable in various industrial enterprises, workshops for metalworking, shipbuilding, printing houses, repair shops, car washes, etc. For this use, certain highly absorbent materials are separated. Textile waste is divided by composition and colour and cut to certain sizes on specialized machines, removing zippers, buttons, collars, cuffs and other hard parts. To ensure the absence of elements that can scratch the surfaces to be cleaned, the rags pass through a metal detector.
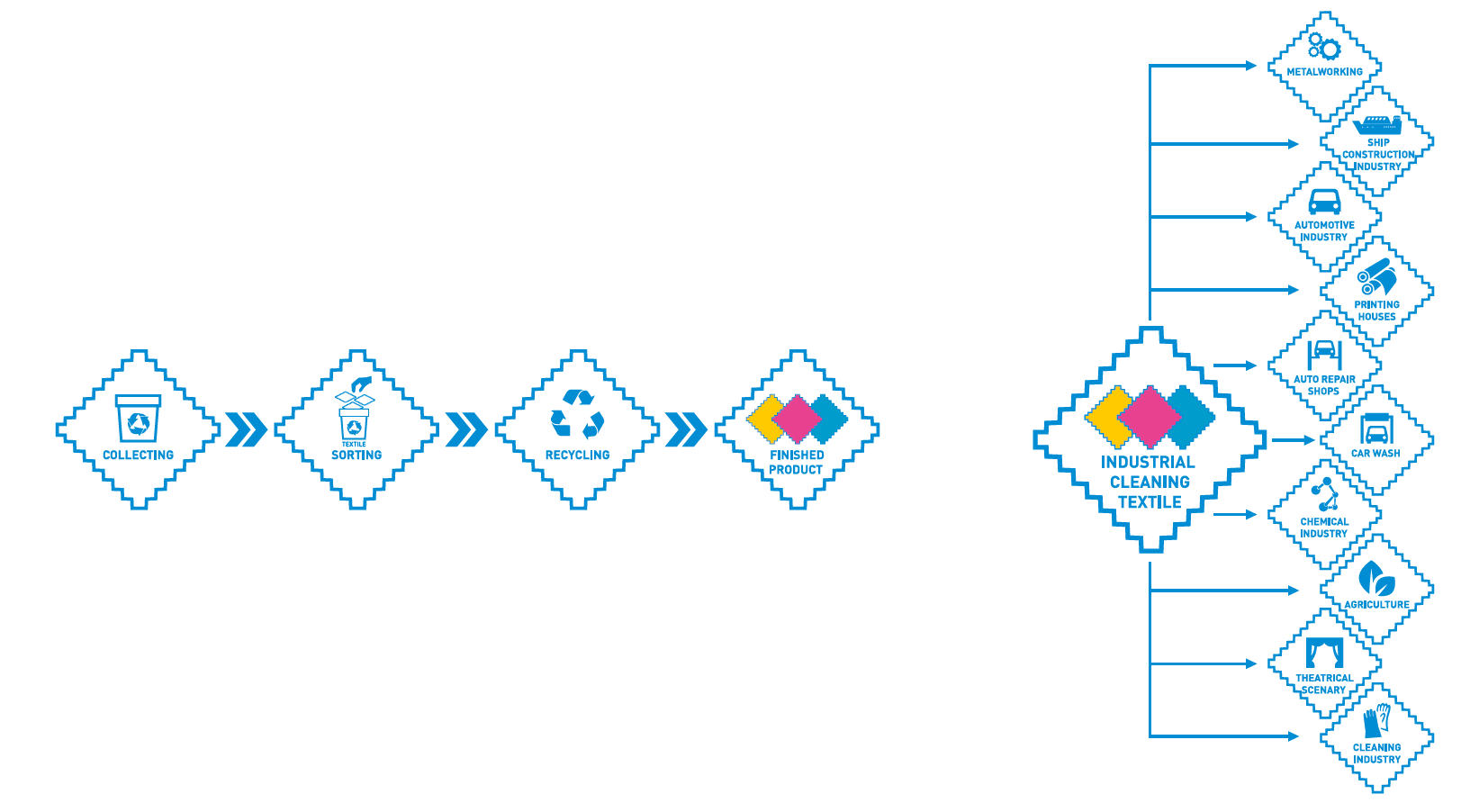
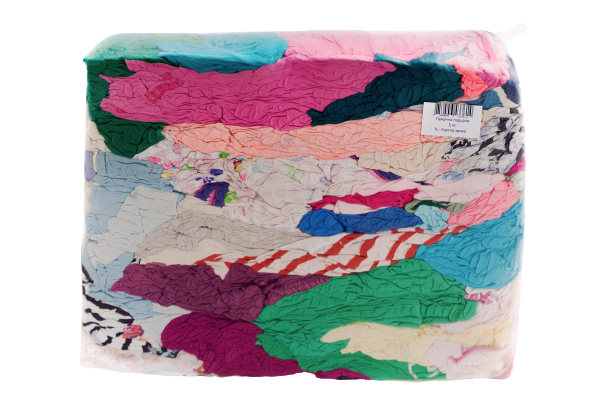
Textile materials that are not suitable for direct reuse, such as clothing or rags and other waste separated during the sorting process (e.g. packaging), are baled and handed over to other companies for proper recycling and recovery. Waste treatment companies are selected according to the environmental methods they use.
Some fabrics (mostly sweaters and other knit products) are being recycled into new yarns in India. Recycling companies in India distribute incoming materials by type and colour. Thanks to the colour separation, there is no need for re-dyeing, which saves energy and reduces the use of pollutants.
The processing process begins with the cutting of the material into “residual fibres”. Depending on the end use of the yarn, other fibres can be added to the residual fibre. The mixture is then carded to clean and blend the fibres and spun into threads ready for weaving and knitting. From these residual fibres, recycling companies produce blankets or sell it directly.
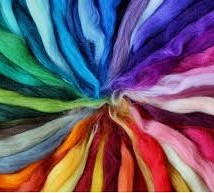
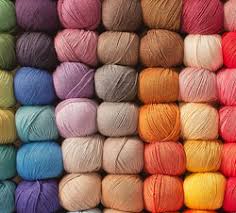
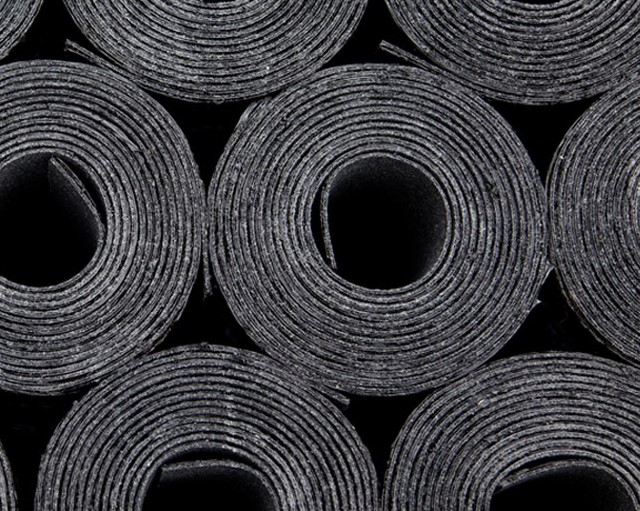
Another part of the unfitted textile materials (e.g. jeans and white textiles) is being sorted by colour, their zippers and buttons are being cut and handed over to installations for the manufacture of wool insulation.
Finely cut textile waste is also used for filling in the manufacture of car seats, sofas, etc.

WHY WE DO IT?
Circular economy is an alternative to the traditional linear economy, following the make - use - dispose scheme, in which we strive to preserve the value of products, materials and resources in the economy for as long as possible. This can be achieved through sustainable design, repair, reuse, refurbishment, reproduction and recycling.
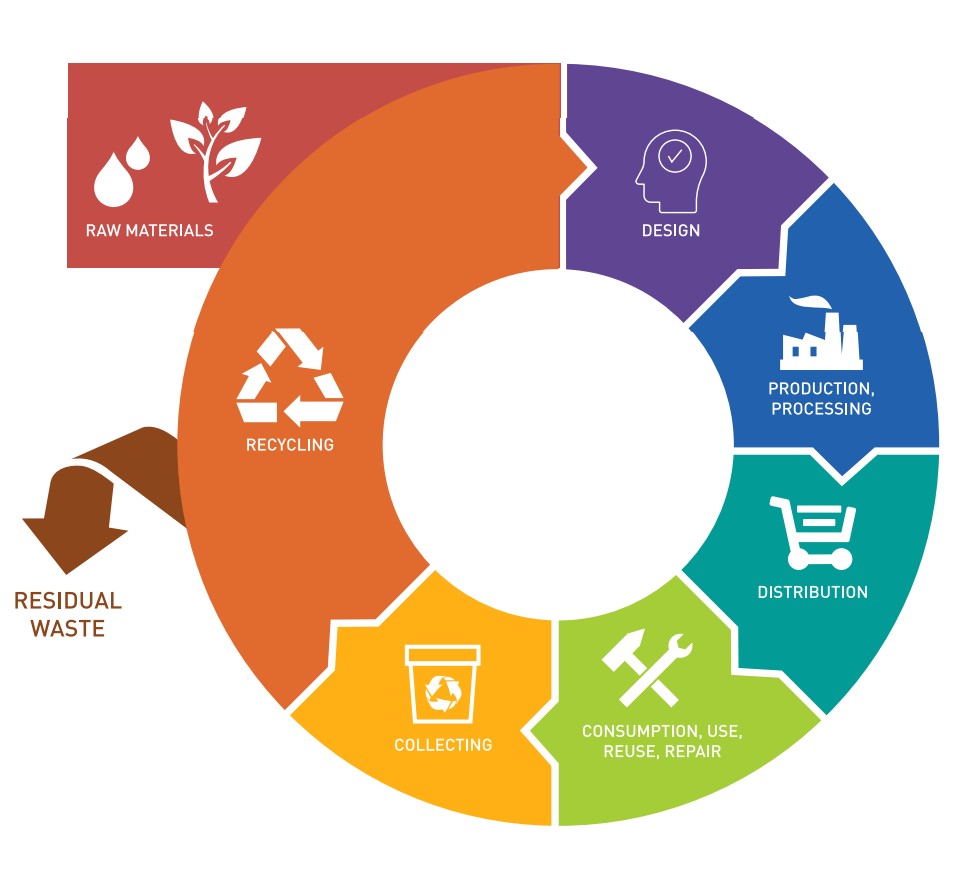
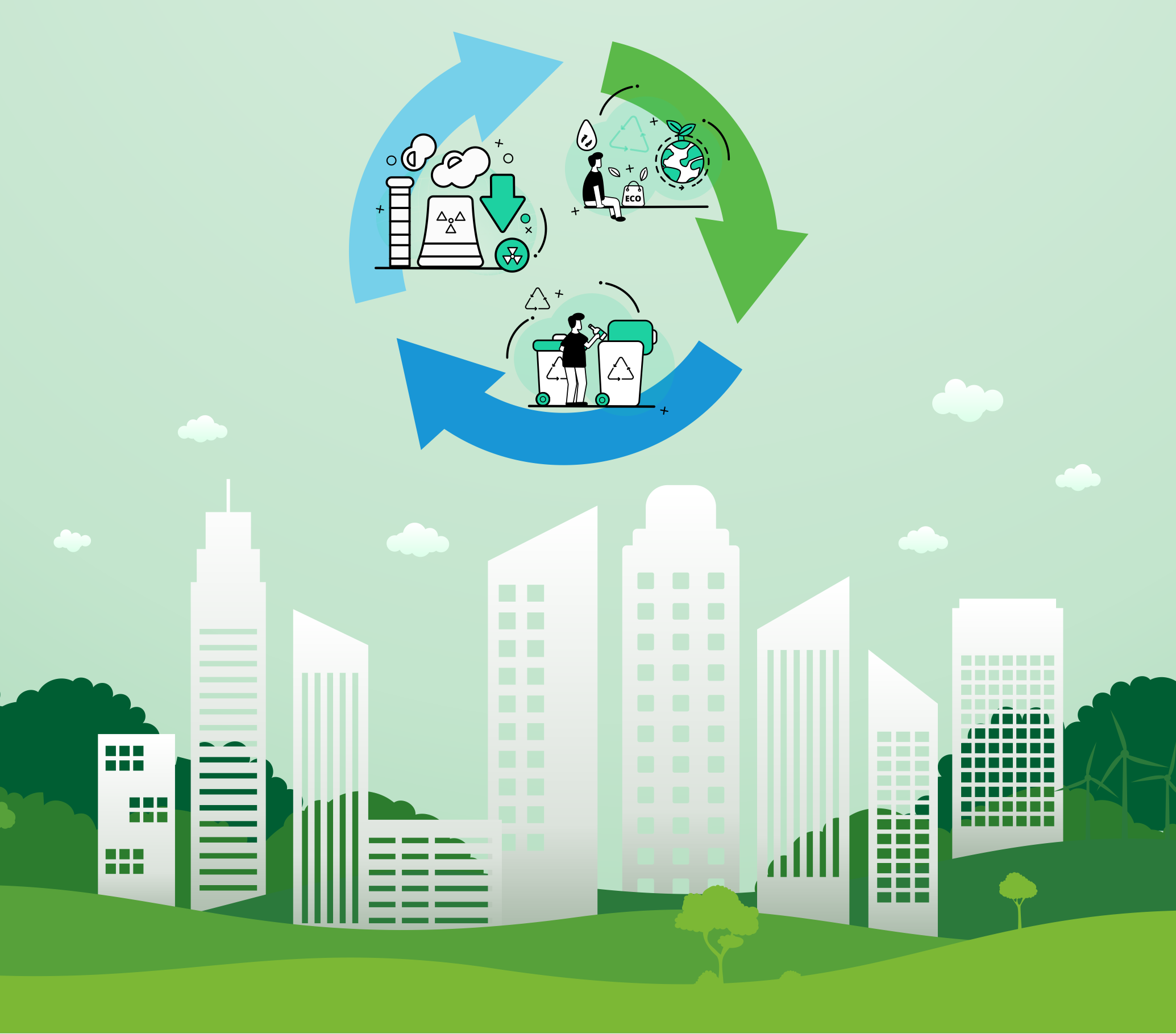
The world‘s population will continue to grow and the world economy will grow at an ever faster pace. The new social and economic challenges will require radical changes in the way we produce, consume and manage waste. In Europe, we are facing difficult challenges. We already import six times more resources than we export. Commodity markets are put under significant pressure, which may increase in the future. The solution is to keep available resources in a productive cycle for a much longer period of time than we are used to. Our future will be related to the use of products and raw materials that can be used repeatedly and do not harm the natural resources of the Earth.
The growing consumption of clothing and the development of the “fast fashion” model are expected to lead to a disastrous increase in environmental damage from the disposal of obsolete textiles. Between 10,000 and 20,000 litres of water are needed to produce a kilogram of cotton, equivalent to the weight of a man's shirt and pair of jeans. Cotton producers account for a quarter of the world's pesticide consumption, and the energy invested in the entire life cycle of clothing used in the EU generates 195 million tonnes of CO2 per year. About 20% of industrial water pollution is associated with dyeing and textile processing. People are buying more and more clothes, reaching 6.4 million tonnes a year in the EU.
Here are the benefits if the textiles you use are collected and recycled instead of sent to landfills:
- The amount of textiles in landfills is reduced, given that synthetic fibres practically do not decompose and the decay of natural ones takes a long time and is associated with the emission of harmful gases
- The harmful impact on the environment in the process of production of new fibres is reduced
- The use of energy, water and primary raw materials for production is reduced
- Less wastewater is generated
- The use of dyes and chemicals is reduced
- Harmful emissions related to all production processes, etc., are reduced
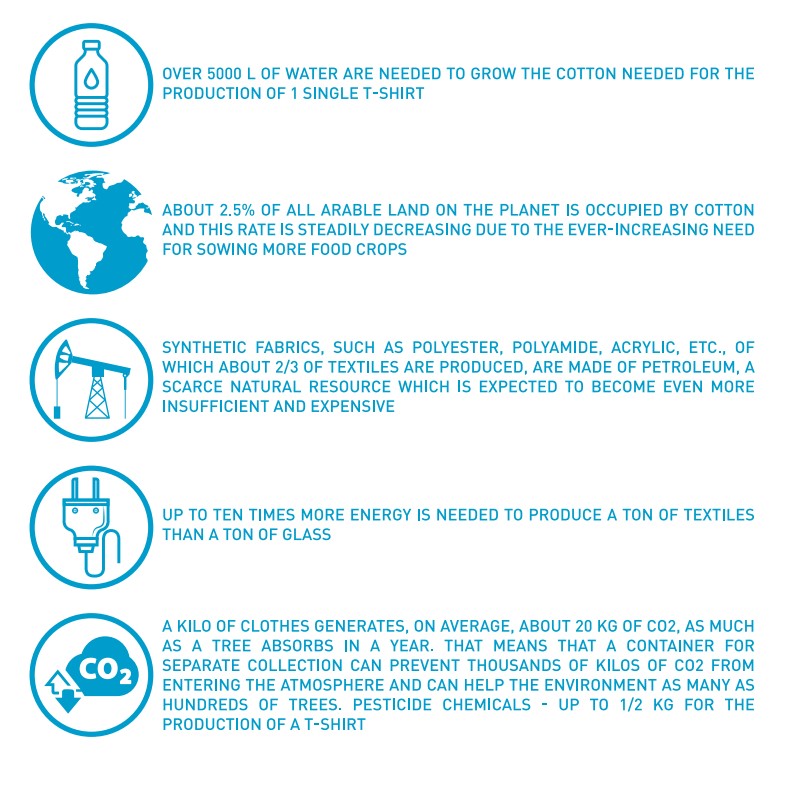
The list can be extended. The following approximate data are eloquent:
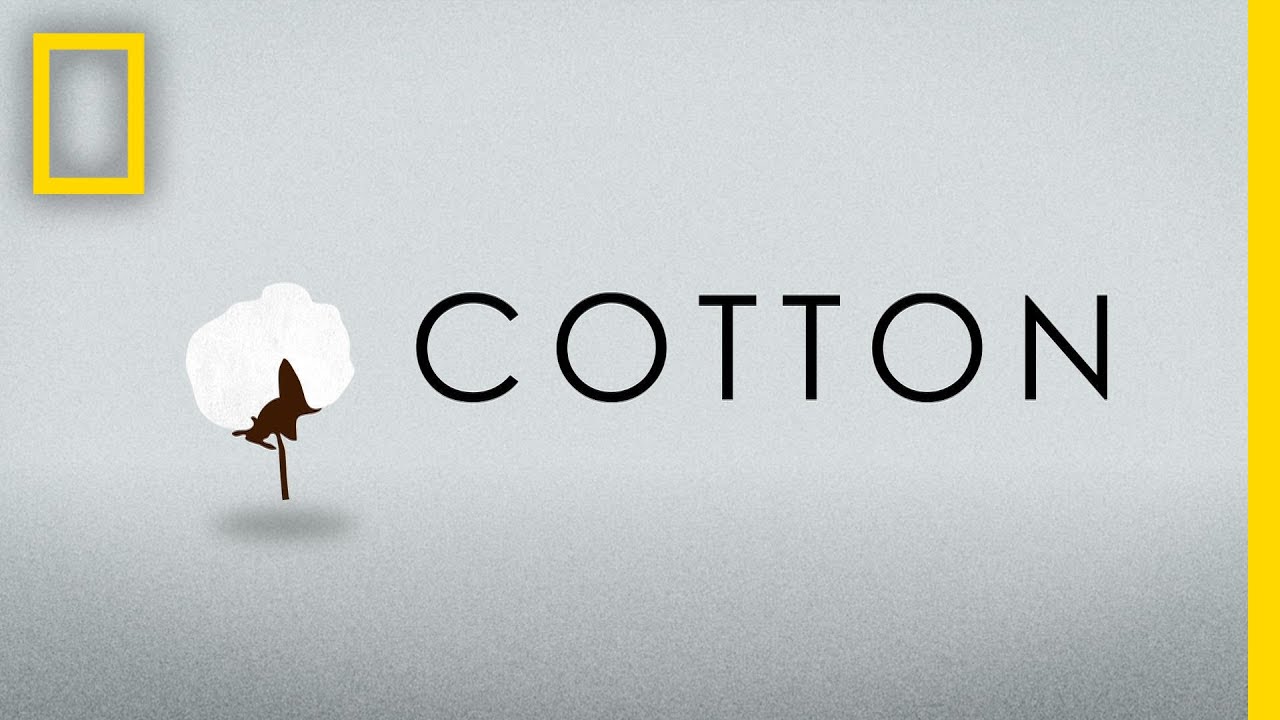